www.engineering-thailand.com
12
'10
Written on Modified on
System solution with RIVTEX
The RIVTEX system solution from Arnold Umformtechnik and Arnold & Shinjo is a high-quality alternative to conventional welding. It cuts parts assembly costs whilst assuring every quality requirement.
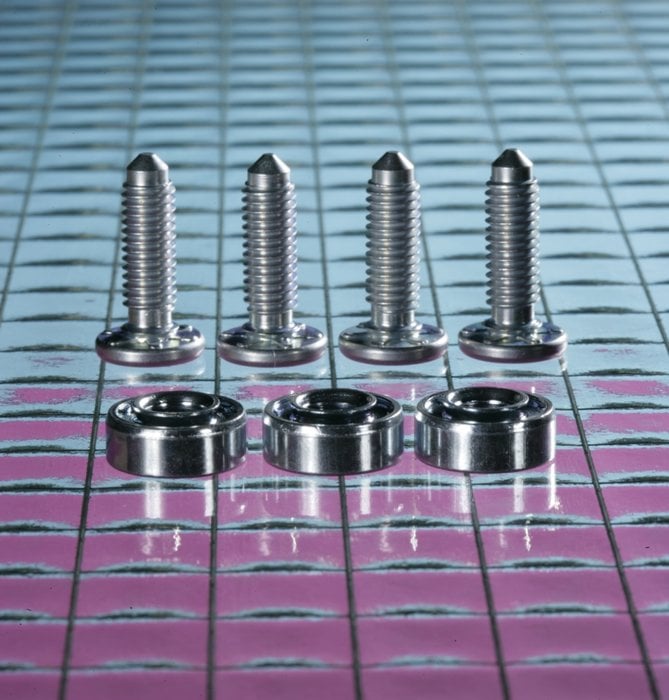
With the RIVTEX system studs and nuts are pressed into the ready-to-assemble sheet metal parts such that they do not fall out and are characterised by high twisting moments and press-out forces. The fastening process, controlled by intelligent tool technology, remains integrated in the press process and replaces at least one complete operation.
Tangible cost reductions in industrial assembly processes can only be made throughout the process chain. Arnold & Shinjo GmbH & Co. KG was set up for this purpose. It offers consultancy and support to customers and supplies the corresponding tool technology. The company offers a package stud/nut solution including a process technology specially tailored to the product benefits.
The RIVTEX range comprises of clinch studs and self-piercing nuts address the requirements arising from steel and aluminium sheets less than 1 millimetre thick. RIVTEX fasteners cannot fall out because they are pressed firmly into the sheet metal component. With their large bonding area, RIVTEX fasteners are extremely stable against press-out forces and torque, and so develop their own safeguard against failure.
RIVTEX fasteners replace welding and the associated environmental hazards. The surface structure around the fastening is protected and there is no welding spatter - so no requirement for additional reworking after application. The risk of corrosion (due to the 90% level of zinc coating in sheet steel welding) can be eliminated with the RIVTEX alternative.
Unlike welding screws and welded nuts, these fasteners can be applied at the same time as the sheet steel is stamped and pressed. Arnold & Shinjo supply standardised tool and feed technology which enable several fasteners to be emplaced in a single stroke. RIVTEX fasteners can be processed on the fast-running tool in exactly the same way as in the transfer press or pressing line.
Fig. 1: The extremely flat, aligned ring supports press the sheet material, assisted by the force-fit punching tool ring, into the locking groove. (Source: Arnold Umformtechnik GmbH)
Fig. 2: The piercing ring punches the hole and squeezes the material into the locking groove. (Source: Arnold Umformtechnik GmbH).
Tangible cost reductions in industrial assembly processes can only be made throughout the process chain. Arnold & Shinjo GmbH & Co. KG was set up for this purpose. It offers consultancy and support to customers and supplies the corresponding tool technology. The company offers a package stud/nut solution including a process technology specially tailored to the product benefits.
The RIVTEX range comprises of clinch studs and self-piercing nuts address the requirements arising from steel and aluminium sheets less than 1 millimetre thick. RIVTEX fasteners cannot fall out because they are pressed firmly into the sheet metal component. With their large bonding area, RIVTEX fasteners are extremely stable against press-out forces and torque, and so develop their own safeguard against failure.
RIVTEX fasteners replace welding and the associated environmental hazards. The surface structure around the fastening is protected and there is no welding spatter - so no requirement for additional reworking after application. The risk of corrosion (due to the 90% level of zinc coating in sheet steel welding) can be eliminated with the RIVTEX alternative.
Unlike welding screws and welded nuts, these fasteners can be applied at the same time as the sheet steel is stamped and pressed. Arnold & Shinjo supply standardised tool and feed technology which enable several fasteners to be emplaced in a single stroke. RIVTEX fasteners can be processed on the fast-running tool in exactly the same way as in the transfer press or pressing line.
Fig. 1: The extremely flat, aligned ring supports press the sheet material, assisted by the force-fit punching tool ring, into the locking groove. (Source: Arnold Umformtechnik GmbH)
Fig. 2: The piercing ring punches the hole and squeezes the material into the locking groove. (Source: Arnold Umformtechnik GmbH).