www.engineering-thailand.com
03
'18
Written on Modified on
ความเป็นจริงของเศรษฐศาสตร์อุตสาหกรรมการผลิตในปัจจุบัน
โรงงานต้องการที่จะผลิตชิ้นงานให้ได้ตามจำนวนและคุณภาพที่ต้องการภายในระยะเวลาและต้นทุนที่กำหนดไว้ การบรรลุเป้าหมายเหล่านั้นได้อย่างสม่ำเสมอนั้นมีความเกี่ยวข้องกับการควบคุมปัจจัยต่างๆ จำนวนมาก ได้แก่ พารามิเตอร์การตัด ต้นทุนเครื่องมือและจำนวนครั้งของการปรับเปลี่ยน การใช้งานเครื่องจักร ค่าใช้จ่ายในการจัดการชิ้นงาน และต้นทุนด้านแรงงานและวัสดุ
เศรษฐศาสตร์การผลิตเป็นศาสตร์และศิลป์ในการทำให้ปัจจัยต่างๆ ในกระบวนการเกิดความสมดุลเพื่อให้บรรลุผลลัพธ์ที่ต้องการ ในช่วงเวลากว่า 2 ศตวรรษที่ผ่านมาของประวัติศาสตร์การตัดเฉือน องค์ประกอบต่างๆ ของเศรษฐศาสตร์การผลิตได้เพิ่มมากขึ้นเป็นทวีคูณ การผลิตได้เริ่มพัฒนาจากการผลิตชิ้นงานด้วยมือทีละชิ้น ไปเป็นการผลิตชิ้นส่วนที่มีมาตรฐานเดียวกันจำนวนมากด้วยเครื่องจักร การปรับปรุงวิธีการผลิตนำมาสู่การผลิตเป็นจำนวนมากในยุคที่สองที่โดดเด่นด้วยสายการผลิตและผลผลิตชิ้นงานที่เหมือนกันในจำนวนที่เพิ่มมากขึ้นเรื่อยๆ ที่เรียกว่า high volume, low product mix (HVLM) (กลุ่มผลิตภัณฑ์มีความหลากหลายต่ำ แต่จำนวนการผลิตสูง) จากนั้นเครื่องจักร CNC และหุ่นยนต์ได้ช่วยให้เกิดระบบการผลิตเป็นจำนวนมากที่มีประสิทธิภาพยุคที่สาม ล่าสุดเทคโนโลยีดิจิตอลที่ใช้ในการโปรแกรม การควบคุมเครื่องจักร และระบบการจัดการชิ้นงาน กำลังก่อให้เกิดอุตสาหกรรมการผลิตในยุคที่สี่ที่รู้จักกันในชื่อว่า อุตสาหกรรม 4.0 ซึ่งช่วยให้เกิดการผลิตที่เรียกว่า high-mix low-volume (HMLV) (สินค้ามีความหลากหลายสูง แต่จำนวนการผลิตต่ำลง) ที่ให้ความคุ้มค่า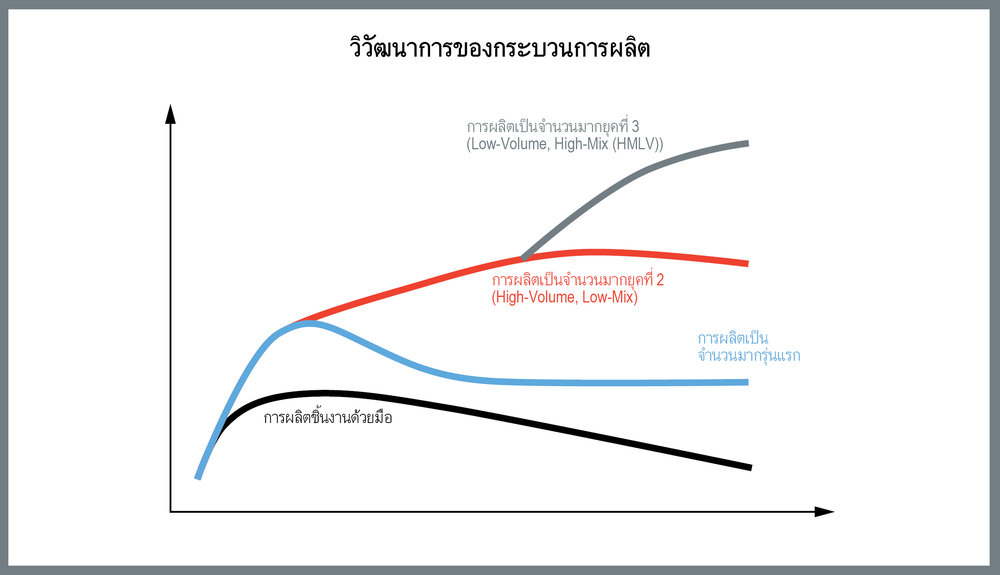
HQ_POS_Manufacturing_Process_Evolution.jpg
สิ่งสำคัญที่จะทำให้ผู้ผลิตประสบความสำเร็จในการเปลี่ยนจากการผลิตแบบ HVLM เป็น HMLV ได้อย่างมีประสิทธิภาพนั้น คือผู้ผลิตต้องตระหนักถึงความเป็นจริงที่กำลังเปลี่ยนแปลงและมีความสำคัญมากขึ้นเรื่อยๆ ของเศรษฐศาสตร์การผลิตและใช้ประโยชน์จากข้อมูลและเทคโนโลยีที่มีอยู่เพื่อวิเคราะห์การดำเนินงานของตนและเพื่อทำให้บรรลุเป้าหมายของตนเอง องค์ประกอบที่สำคัญอย่างหนึ่งของการปรับโฉมการผลิตดังกล่าวนี้มีความเกี่ยวข้องกับการละทิ้งความเชื่อและแนวปฏิบัติที่ฟังดูง่ายเกินไปและการค้นหาต้นทุนที่ซ่อนอยู่ที่อาจบ่อนทำลายความพยายามในการเพิ่มประสิทธิภาพการผลิตให้สูงสุด
จำนวนการผลิตสูง ความหลากหลายต่ำ เศรษฐศาสตร์ง่ายๆ อย่างไร
กระบวนการตัดเฉือนที่เป็นมาตรฐานได้รับการพัฒนาขึ้นมาในศตวรรษที่ 19 เพื่อเพิ่มความเร็วในการผลิตสินค้าที่มีความเหมือนกันที่สามารถเปลี่ยนชิ้นส่วนได้ การผลิตด้านยานยนต์ได้ทำให้วิธีการ HVLM นี้ก้าวสู่ระดับสูงสุด โดยก่อตั้งระบบสายพานการผลิต (transfer lines) และวิธีการอื่นๆ ที่ผลิตชิ้นส่วนเดียวกันนั้นเป็นจำนวนมากหรือหลายล้านชิ้นออกมาซ้ำๆ ในแต่ละปี
ลักษณะของการผลิตแบบ HVLM ในระยะยาวช่วยให้ผู้ผลิตสามารถปรับเปลี่ยนปัจจัยต่างๆ ในกระบวนการเพื่อให้ได้รับผลผลิตสูงสุด สม่ำเสมอ และต้นทุนต่ำ เทคโนโลยีเสริมรวมถึงเครื่องมือและเครื่องเปลี่ยนพาเลทและหุ่นยนต์ยังช่วยลดความผันแปรลงไปได้อีก โดยเป็นที่เข้าใจกันว่าการดำเนินการเป็นไปอย่างสมบูรณ์แบบและให้ผลผลิตแบบ 100% พร้อมกับสามารถคาดการณ์ต้นทุนได้ ไม่เกิดการหยุดทำงานที่ไม่ต้องการ ไม่มีผลผลิตที่เสียไป ไม่ต้องแก้ไขชิ้นงาน และไม่มีการดำเนินการในขั้นตอนต่อมา เช่น การลบคมของชิ้นงาน เป็นต้น
มีความเข้าใจกันอย่างหนึ่งว่าต้นทุนเครื่องมือโดยทั่วไปแล้วมีราว 3% ของต้นทุนการผลิตทั้งหมด จำนวน 3% ดังกล่าวนี้เป็นเกณฑ์มาตรฐานที่ง่ายดายแต่แทบจะไม่ถูกต้องเลย ตัวอย่างเช่น ลักษณะของการกลึงวัสดุชิ้นงานมีผลอย่างมาก การเปลี่ยนจากเหล็กกล้าเป็นไทเทเนียมในการกลึงชิ้นงานสามารถเพิ่มการใช้งานเครื่องมือขึ้นอีกถึง 5 เท่า ทำให้สัดส่วน 3% ดังกล่าวนี้กลายเป็น 15% หากไม่มีปัจจัยอย่างอื่นก่อให้เกิดการเปลี่ยนแปลง
การมุ่งเน้นไปที่เวลาบริหารจัดการเรื่องเครื่องมือเพียงอย่างเดียวทำให้ละเลยปัจจัยอื่นๆ เช่น เวลาหยุดทำงานเพื่อเปลี่ยนเครื่องมือ วิธีการนี้ปกปิดให้มองไม่เห็นความจริงอย่างได้ผล ผู้ผลิตควรเข้าใจว่าเวลาในการตัดเฉือน เวลาในการจัดเตรียม เวลาในการเปลี่ยนเครื่องมือ การโหลดและการถ่ายเทชิ้นงาน และปัจจัยอื่นๆ ที่ส่งผลกระทบและรบกวนซึ่งกันและกัน
ตัวอย่างง่ายๆ ของการเผชิญกับปัจจัยต่างๆ ในกระบวนการโดยที่ไม่ได้คาดคิดมาก่อน คือโรงงานแห่งหนึ่งทำการตัดเฉือนชิ้นส่วนที่ต้องใช้เวลา 2 นาทีในการตัดเฉือน และเวลารวม 2 นาทีในการโหลดและการถ่ายเทชิ้นงาน การทำดัชนีเครื่องมือใช้เวลา 1 นาที และอายุการใช้งานเครื่องมือเท่ากับ 5 ชิ้นงาน ทำให้เวลาในการทำดัชนีเครื่องมือเท่ากับ 0.20 นาทีต่อชิ้นส่วน เนื่องจากทุกชิ้นส่วนต้องใช้เวลาในการดำเนินการ 4.2 นาที ผลผลิตที่ได้มากกว่า 14 ชิ้นงานเล็กน้อยต่อชั่วโมง เครื่องมือแต่ละชิ้นมีต้นทุน 15 ยูโร และอายุการใช้งานเครื่องมือเท่ากับ 5 ชิ้นงาน ทำให้ต้องใช้เครื่องมือ 2.8 ชิ้น (เท่ากับ 42 ยูโร) ในการผลิต 14 ชิ้นงาน ต้นทุนด้านเครื่องจักรคือ 50 ยูโรต่อชั่วโมง ทั้งหมดทั้งมวลแล้วต้นทุนการผลิตสำหรับ 14 ชิ้นงานในหนึ่งชั่วโมงคือ 92 ยูโร
จากนั้น โรงงานดังกล่าวนี้พยายามเร่งความเร็วในการผลิตและประสิทธิภาพในการทำงาน โดยได้เพิ่มความเร็วในการตัดเฉือนขึ้นอีก 10% ซึ่งช่วยลดเวลาในการตัดเฉือนลงได้ 10% (1.8 นาที) แต่ยังเป็นการลดอายุการใช้งานเครื่องมือลงครึ่งหนึ่งโดยประมาณ ซึ่งหมายความว่า 1 คมตัดจะผลิตได้เพียง 2 ชิ้นงานครึ่งเท่านั้นก่อนที่จะต้องมีการทำดัชนี เวลาในการทำดัชนีเครื่องมือยังคงเป็น 1 นาทีและการโหลด/การถ่ายเทชิ้นงาน 2 นาที เวลาในการผลิตสำหรับ 1 ชิ้นงานยังคงเป็น 4.2 นาที (1.8 นาทีในการตัดเฉือน, 2 นาทีในการจัดการชิ้นงาน และ 0.4 นาทีในการทำดัชนีเครื่องมือ) หรือ 14 ชิ้นงานต่อชั่วโมง ต้นทุนเครื่องจักรและเครื่องมือยังคงเดิม แต่ตอนนี้ต้องใช้เครื่องมือ 5.6 ชิ้น (ต้นทุนเครื่องมือ 84 ยูโร) ในการรันเป็นเวลา 1 ชั่วโมง แม้ว่าจะพยายามเพิ่มความเร็วในการผลิต แต่เวลาในการผลิตสำหรับ 14 ชิ้นงานยังคงเท่าเดิม และต้นทุนได้เพิ่มขึ้นจาก 92 ยูโรเป็น 134 ยูโร
ในกรณีนี้ การเพิ่มความเร็วในการตัดเฉือนไม่ได้ทำให้การผลิตมีประสิทธิภาพมากขึ้น เวลาในการตัดเฉือนที่เปลี่ยนแปลงไปส่งผลกระทบต่อปัจจัยอื่นๆ ในระบบการตัดเฉือน ซึ่งในตัวอย่างนี้ได้แก่อายุการใช้งานเครื่องมือและเวลาในการทำดัชนีเครื่องมือ ดังนั้นโรงงานต้องพิจารณาอย่างรอบคอบเกี่ยวกับผลที่ตามมาทั้งหมดของการเปลี่ยนแปลงกระบวนการ
อีกรูปแบบหนึ่งของต้นทุนที่ซ่อนอยู่เกี่ยวข้องกับขั้นตอนต่างๆ ในกระบวนการ ตัวอย่างเช่น ในโรงงานจำนวนมาก เวลาที่ใช้ในการทำดัชนีเม็ดมีดเป็นตัวอย่างที่ชัดเจนเกี่ยวกับต้นทุนที่ซ่อนอยู่ เวลาที่กำหนดไว้เพื่อทำดัชนีเม็ดมีดอาจเป็น 1 นาที อย่างไรก็ตาม เมื่อวัดตามจริงในพื้นที่การทำงาน เวลาที่ใช้จริงอาจเป็น 2, 3 หรือ 10 นาที เป็นความแตกต่างระหว่าง 60 วินาทีจนถึง 600 วินาที
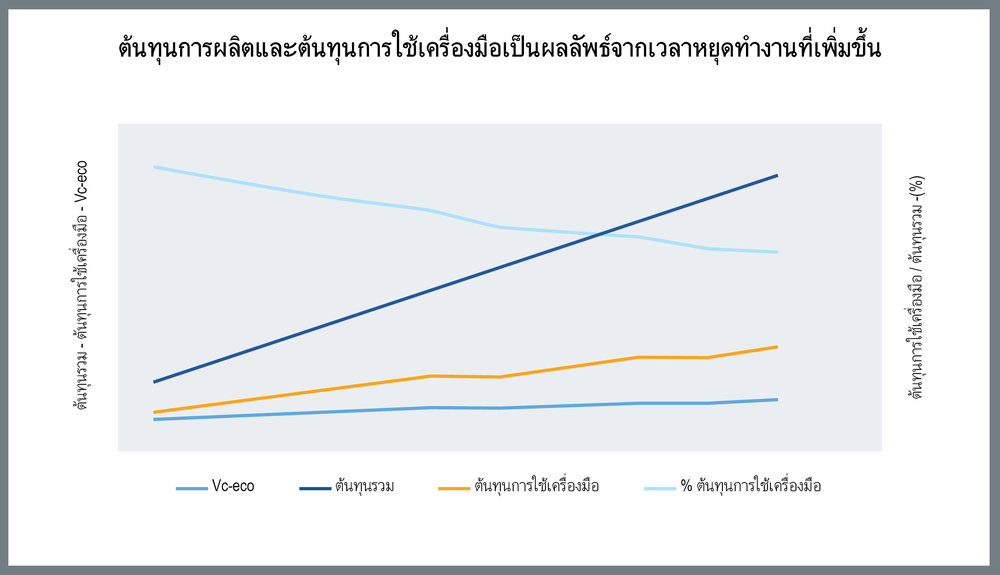
HQ_ILL_Production_Cost_And_Tooling_As_A_Function_Of_Increasing_Idle_Times.jpg
รูปที่ 2
ความหลากหลายสูง จำนวนการผลิตต่ำลง ข้อพิจารณาที่ซับซ้อน
เมื่อไม่นานมานี้ การแข่งขันทั่วโลกกำลังกระตุ้นให้ผู้ผลิตสร้างสรรค์ผลิตภัณฑ์ของตนในเวอร์ชันต่างๆ เพื่อให้ตรงกับความต้องการของกลุ่มย่อยผู้ใช้ที่เล็กลง เทคโนโลยีคอมพิวเตอร์ขั้นสูงช่วยให้การออกแบบชิ้นส่วนและโปรแกรมการตัดเฉือนเกิดการเปลี่ยนแปลงอย่างรวดเร็ว และยังช่วยให้ติดตามความหลากหลายของผลิตภัณฑ์และคลังสินค้าได้อย่างง่ายดาย เป็นผลทำให้เกิดการเปลี่ยนไปสู่สถานการณ์การผลิตที่เรียกว่า higher mix, lower volume (HMLV) (สินค้ามีความหลากหลายสูง แต่จำนวนการผลิตต่ำลง) ทุกวันนี้วิธีการดังกล่าวนี้ได้รับการพัฒนาจนเพียงพอที่จะทำให้เกิดการผลิตที่มีประสิทธิภาพที่เรียกว่า Single-Digit Production หรือแม้แต่ Single-Item Production
ขอบเขตการวางแผนที่มีระยะเวลายาวนานขึ้นของการผลิตแบบ HVLM ช่วยให้มีการวางแผนอย่างรอบคอบไม่เร่งรีบและมีการปรับเปลี่ยนปัจจัยต่างๆ ในกระบวนการเป็นอย่างดี แต่การวางแผนในสถานการณ์การผลิตแบบ HMLV มีความแตกต่างออกไป เทคโนโลยีวิศวกรรมในระบบคอมพิวเตอร์และคลังสินค้าสนับสนุนให้เกิดการเปลี่ยนแปลงอย่างรวดเร็วในด้านประเภทผลิตภัณฑ์และผลผลิต แต่ผลที่ตามมาคือ กระบวนการวางแผนของ HMLV ต้องซับซ้อนและตอบสนอง คำสั่งซื้อชิ้นส่วน 10 ชิ้นอาจตามมาด้วยจำนวน 2 หรือ 5 ล็อตของชิ้นส่วนที่แตกต่างกัน หรือแม้แต่ล็อตแบบ Single-Item ของชิ้นส่วนที่แตกต่างกัน วัสดุชิ้นงานอาจเปลี่ยนจากเหล็กกล้าเป็นอะลูมิเนียมเป็นไทเทเนียม และรูปทรงของชิ้นส่วนอาจเปลี่ยนจากง่ายเป็นซับซ้อน ไม่มีเวลาเพียงพอที่จะกำหนดอายุการใช้งานเครื่องมือผ่านการทดลองใช้
ในการจัดการอายุการใช้งานเครื่องมือในสถานการณ์แบบ HMLV โรงงานมักจะทำการคาดเดาตามแบบอนุรักษ์นิยมที่ทำกันมาเกี่ยวกับอายุการใช้งานที่คาดไว้ของเครื่องมือ และเพื่อความปลอดภัย จะใช้เครื่องมือใหม่สำหรับการรันแต่ละครั้ง ทิ้งเครื่องมือก่อนที่เครื่องมือจะมีอายุถึงการใช้งานได้เต็มประสิทธิภาพ เวลาในการตัดเฉือนเป็นเพียงปัจจัยหนึ่งเท่านั้นในภาพรวม ในการผลิตแบบ HMLV เวลาที่ต้องใช้ในการจัดการชิ้นงานต่างๆ และอุปกรณ์ปรับตั้ง เปลี่ยนเครื่องมือและทำดัชนีเม็ดมีด มักจะนานกว่าเวลาในการตัดเฉือนจริง ปัจจัยด้านการใช้เครื่องมือ เครื่องจักร เวลาในการหยุดทำงาน แรงงานทางตรง และวัสดุชิ้นงาน อาจมีต้นทุนที่ซ่อนอยู่ วิธีการล่าสุดในเรื่องเศรษฐศาสตร์การผลิตจะพิจารณาต้นทุนเครื่องมือและวัสดุชิ้นงาน ต้นทุนอุปกรณ์และการผลิต ต้นทุนอุปกรณ์ในระหว่างที่หยุดทำงานและต้นทุนเงินเดือนและการบำรุงรักษาด้วย
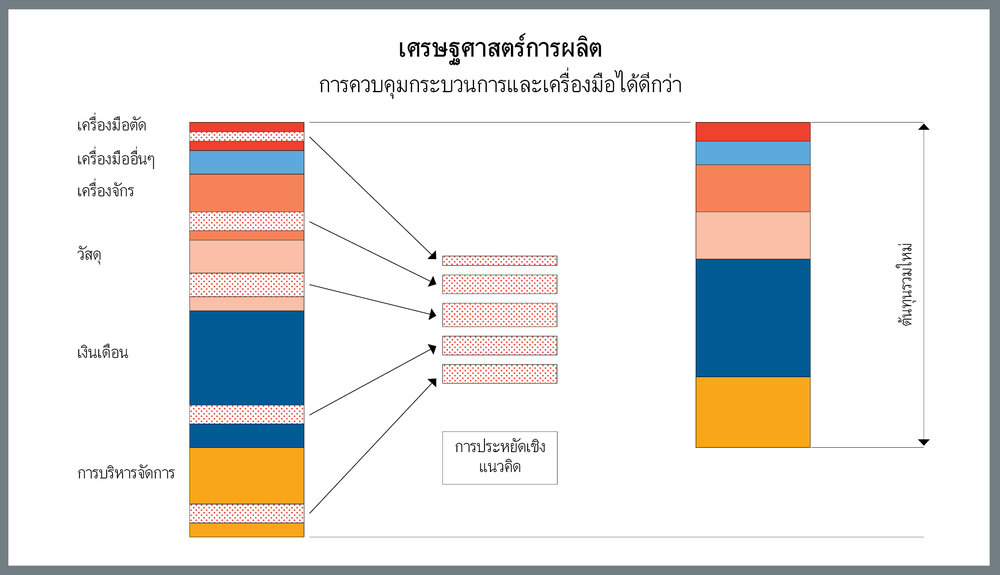
HQ_ILL_Production_Economics
รูปที่ 3
ข้อกำหนดในการผลิตแบบ HMLV ที่มีการเปลี่ยนแปลงอย่างรวดเร็ว ทำให้การได้ผลผลิตเป็นเปอร์เซ็นต์สูงยากมากขึ้นไปอีก ในกรณีของการผลิตแบบ HVLM ที่มีเวลาในระยะยาวนั้น การทดลองและการปรับเปลี่ยนสามารถสร้างผลผลิตได้สูงถึง 90% ในทางตรงกันข้าม ผลผลิตของ HMLV อาจเป็นสองส่วน การรันชิ้นส่วนเดียวที่ประสบความสำเร็จเป็นผลผลิต 100% แต่หากชิ้นส่วนนั้นไม่สามารถใช้ได้หรือชิ้นงานพังเสียหาย ผลผลิตจะกลายเป็นศูนย์ ความต้องการด้านคุณภาพและต้นทุนและประสิทธิภาพด้านเวลานั้นยังคงเหมือนกัน แต่ผลผลิตในครั้งแรกกลายเป็นข้อกำหนดที่สำคัญกว่า ในกรณีดังกล่าว การหลีกเลี่ยงไม่ให้เครื่องมือเสียหายอาจเป็นข้อพิจารณาที่มีความสำคัญมากที่สุด ข้อดีอย่างหนึ่งคือการสึกหรอของเครื่องมือเป็นสิ่งที่ต้องกังวลน้อยมากในการรันในระยะสั้นและโรงงานสามารถใช้พารามิเตอร์การตัดที่เข้มงวดและได้ประสิทธิผลยิ่งขึ้น ทั้งนี้เป็นไปด้วยเหตุผล
ตัวแปรที่เกี่ยวข้องเป็นสิ่งที่กำหนดเวลาที่เหมาะสมในการทำดัชนีเครื่องมือ การรอนานเกินไปอาจทำให้เครื่องมือพังเสียหายและการผลิตเกิดการหยุดชะงักเป็นอย่างน้อยหากชิ้นงานไม่ได้เสียหายไปด้วย ในทางตรงกันข้ามการเปลี่ยนเครื่องมือบ่อยเกินไปจะเพิ่มค่าใช้จ่ายในด้านต้นทุนเครื่องมือเอง เช่นเดียวกับเวลาที่เสียไปในการหยุดการตัดเฉือนและในการทำดัชนีเครื่องมือ การกำหนดเวลาในการเปลี่ยนเครื่องมือจำเป็นต้องมีการตรวจสอบความสัมพันธ์ของการเปลี่ยนกับระบบการตัดเฉือนทั้งระบบ การสร้างเกณฑ์วิธีการเปลี่ยนเครื่องมือและการมีวินัยในการปฏิบัติตาม
บทสรุป
ความสัมพันธ์ของปัจจัยต่างๆ ในระบบการตัดโลหะไม่ได้เป็นแบบหนึ่งต่อหนึ่ง สภาวะการตัดเฉือนที่เปลี่ยนแปลง วัสดุชิ้นงาน หรือระดับการผลิตจะส่งผลต่ออายุการใช้งานเครื่องมือ รวมทั้งแง่มุมอื่นๆ จำนวนมากของระบบการตัดเฉือน ความท้าทายสำหรับเศรษฐศาสตร์การผลิตในโรงงานผลิต คือการตระหนักรู้ถึงความสัมพันธ์เหล่านั้นและพัฒนากลยุทธ์เพื่อทำงานกับความสัมพันธ์เหล่านั้นในลักษณะที่เน้นการปฏิบัติ น่าเสียดายที่คนงานในทุกโรงงานไม่สามารถเป็นศาสตราจารย์ในทางคณิตศาสตร์และไม่มีเวลาที่จะมาสำรวจความสัมพันธ์ต่างๆ อย่างเจาะลึกได้ ผลก็คือซัพพลายเออร์เป็นผู้เสนอการวิเคราะห์กระบวนการและบริการด้านการจัดการ (ดูแถบข้าง) ที่ทำให้ผู้ผลิตมองเห็นภาพที่ครอบคลุมเกี่ยวกับการดำเนินการที่เฉพาะเจาะจงของตนและเป็นแนวทางเกี่ยวกับวิธีที่จะเพิ่มความสามารถในการผลิตและจุดแข็งทางเศรษฐกิจของความพยายามของตนให้สูงสุด
ปัญหาประจำสำหรับเจ้าของโรงงาน คือพวกเขาได้งานจำนวนมากและมีลูกค้าที่พร้อมจ่าย แต่ยังคงสูญเสียรายได้ไป วิธีแก้ปัญหาของเจ้าของโรงงาน คือการรับรู้ความเป็นจริงของปัจจัยต่างๆ จำนวนมากในการทำงาน ในด้านเศรษฐศาสตร์การผลิตในปัจจุบัน และการค้นหาและขจัด
ต้นทุนที่ได้ละเลยและซ่อนอยู่ เพื่อให้อุตสาหกรรมการผลิตของพวกเขาสามารถมีกำไรสูงสุด
แถบข้าง
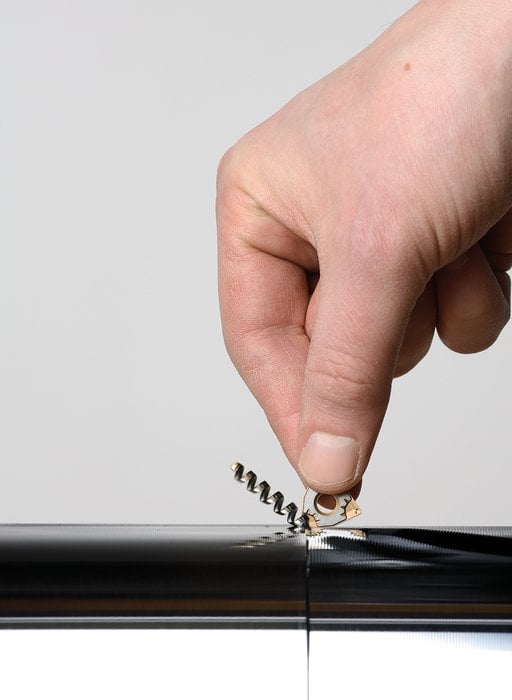
HQ_IMG_Duratomic_Chip.jpg
รูปที่ 4
การวิเคราะห์โดยอัตโนมัติ
นับจากยุคแรกๆ ของการผลิตเป็นจำนวนมาก ปัจจัยต่างๆ จำนวนหนึ่งที่ส่งผลกระทบต่อความสามารถในการผลิตและต้นทุนของอุตสาหกรรมการผลิต ได้เพิ่มขึ้นหลายเท่าตัวเมื่อเวลาผ่านไป การดำเนินการและอุปกรณ์ด้านการตัดเฉือนมีความซับซ้อนมากยิ่งขึ้น ความสัมพันธ์ระหว่างองค์ประกอบต่างๆ ของระบบการผลิตก็ซับซ้อนเช่นกัน ไม่มีองค์ประกอบใดที่ดำรงอยู่ด้วยตัวเอง ตัวอย่างเช่น ข้อกำหนดด้านจำนวนการผลิตที่เปลี่ยนแปลงจะส่งผลต่อต้นทุนการใช้เครื่องมือ อุปกรณ์ การบำรุงรักษา แรงงาน และต้นทุนอื่นๆ
การกำหนดจำนวนของปัจจัยที่เกี่ยวข้องและความสัมพันธ์ระหว่างปัจจัยเหล่านั้นเองคือความท้าทายที่สำคัญ ความซับซ้อนจำเป็นต้องใช้วิธีการที่เป็นระบบในการวัด ควบคุม และจัดการกระบวนการผลิต
ระบบการวิเคราะห์ต้นทุนความสามารถในการผลิต (Productivity Cost Analysis (PCA) ของ Seco จะตรวจสอบกระบวนการผลิตทั้งหมดเพื่อกำหนดวิธีที่จะลดต้นทุนและเพิ่มความสามารถในการผลิต พื้นฐานของระบบดังกล่าวนี้มาจากประสบการณ์และความรู้ด้านการผลิตทั่วโลกเป็นเวลาหลายทศวรรษของ Seco โดย Seco ใช้ความรู้ดังกล่าวผนวกกับการวิเคราะห์ด้วยคอมพิวเตอร์และกระบวนการแก้ปัญหาอย่างเป็นขั้นตอนที่ลุ่มลึก รวมถึงเทคนิคการจำลอง Monte Carlo ที่ทำให้การสร้างโมเดลต้นทุนเป็นระบบอัตโนมัติ
ตัวแทนที่มีความสามารถของ Seco จะทำ PCA ซึ่งประเมินเครื่องมือและเทคโนโลยีทั้งหมดที่ใช้ในกระบวนการ เพื่อสร้างรายงานที่มีข้อมูลครอบคลุม ซึ่งประกอบด้วยทั้งข้อมูลกระบวนการ เช่น ข้อมูลการใช้เครื่องมือและข้อมูลการตัดเฉือน และข้อมูลต้นทุนที่ครอบคลุมต้นทุนต่อชิ้นส่วน ผลผลิตต่อชั่วโมง และต้นทุนด้านการลงทุน โดย PCA สามารถประเมินกระบวนการตั้งแต่การทำงานของเครื่องจักรเดียวไปจนถึงเส้นทางทั้งหมดของชิ้นงานในกระบวนการผลิตของโรงงาน
ระบบการวิเคราะห์ดังกล่าวนี้จะมุ่งเน้นไปที่การเพิ่มประสิทธิภาพของความสามารถในการผลิตที่มีผลกระทบต่อต้นทุนมากที่สุด ระบบจะนำปัญหาคอขวดหรือการติดขัดของการดำเนินการมาพิจารณาและสามารถรู้ถึงจุดที่จำเป็นต้องมีการศึกษาเพิ่มเติมในเชิงลึกยิ่งขึ้น
โดยการทำงานจากเวลาและการศึกษาเกณฑ์มาตรฐานต้นทุนของการดำเนินการหรือโรงงานเป้าหมาย ในขั้นต้นซอฟต์แวร์ PCA จะตรวจสอบปัจจัยต่างๆ ด้านการใช้เครื่องมือ ซึ่งรวมถึงพารามิเตอร์กระบวนการ รอบเวลาของรอบการทำงาน และข้อกำหนดของปริมาณงาน ขั้นที่สองจะเกี่ยวข้องกับกระบวนการเดียวกันนั้นแต่จะทำการปรับในเรื่องสภาวะการตัดเฉือนและเครื่องมือที่กำลังใช้งานอยู่ ขั้นที่สามสามารถเกี่ยวข้องกับการเปลี่ยนแปลงกระบวนการ การรวมการทำงาน และการสำรวจการเปลี่ยนแปลงในระดับที่ใหญ่กว่า เช่น การอัพเกรดเครื่องจักร
โดยทั่วไปแล้วผู้ผลิตที่ใช้ระบบ PCA ของ Seco สามารถคาดหวังที่จะได้รับประโยชน์จากการประหยัดต้นทุนทั้งหมดได้ถึง 30% และความสามารถในการผลิตเพิ่มขึ้นถึง 40% ไม่ว่าจะเป็นภาคอุตสาหกรรมใดก็ตาม
โดย:
Patrick de Vos ผู้จัดการฝ่ายการศึกษาทางเทคนิคของบริษัท Seco Tools