www.engineering-thailand.com
03
'18
Written on Modified on
การวิเคราะห์การเสื่อมสภาพของเครื่องมือโดยรวมที่มองไปไกลกว่าการตัดเฉือน
เครื่องมือตัดคือองค์ประกอบขั้นพื้นฐานของกระบวนการตัดเฉือนโลหะ ทั้งนี้ขึ้นอยู่กับการเลือกและการนำเครื่องมือมาใช้ เครื่องมือตัดสามารถให้ศักยภาพที่จะเพิ่มประสิทธิภาพสูงสุด หรือในทางกลับกันก็เป็นปัญหาคอขวดในการผลิต สิ่งสำคัญคือวิธีจัดการเครื่องมือให้สัมพันธ์กับกระบวนการผลิตโดยรวม
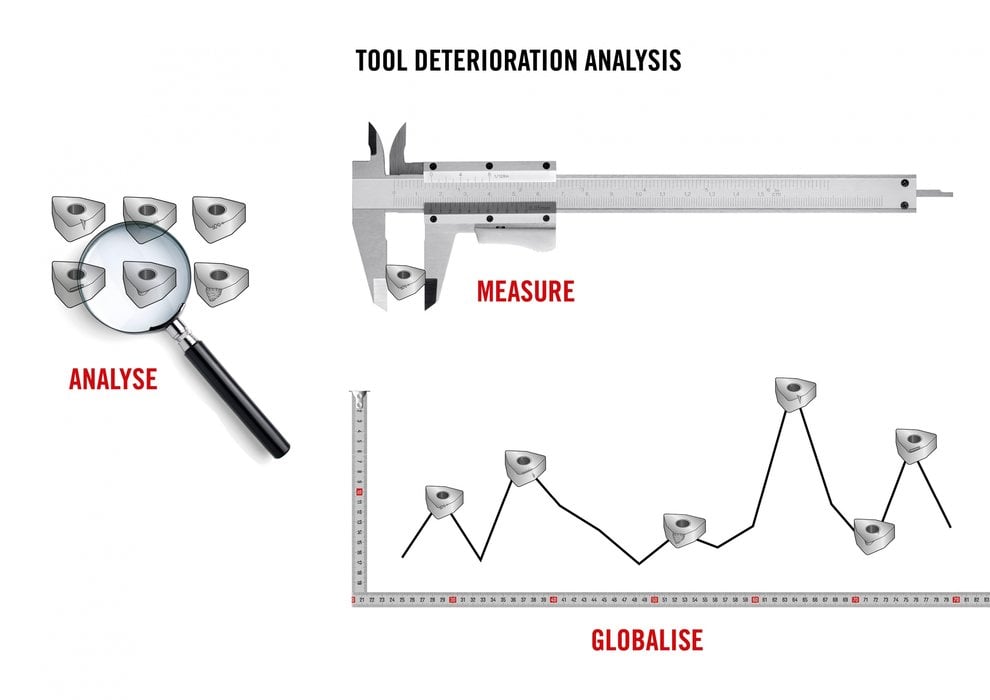
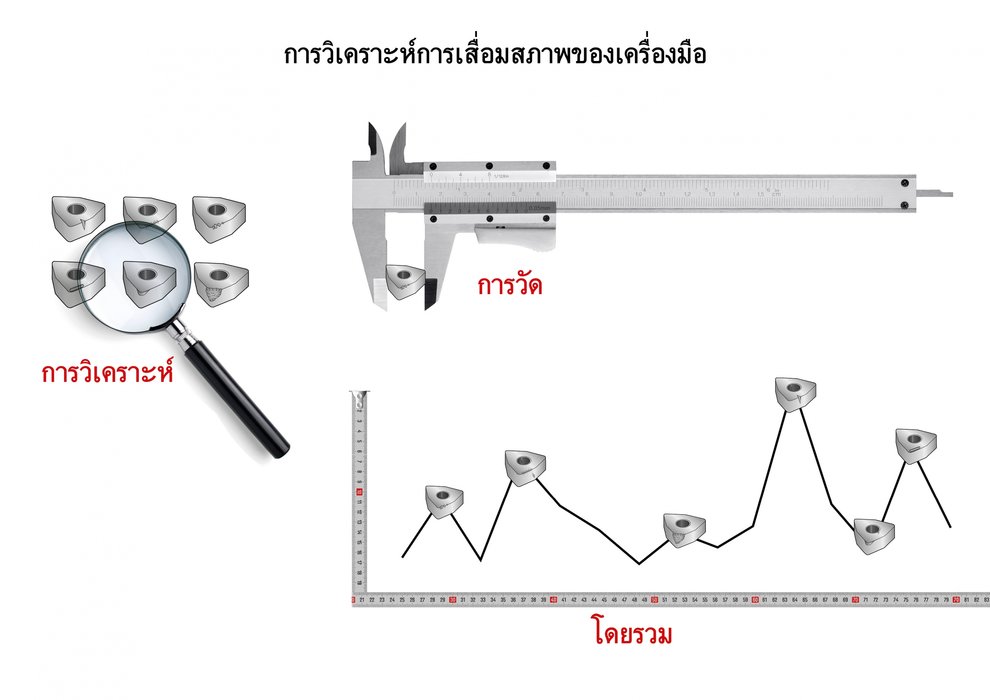
รูปที่ 1
โดยธรรมชาติแล้วเครื่องมือตัดถือเป็นของใช้สิ้นเปลือง เนื่องจากพวกมันจะสึกหรอจนกระทั่งไม่สามารถทำงานได้อย่างมีประสิทธิภาพอีกต่อไป วิธีการดั้งเดิมในการจัดการเครื่องมือตัดเฉือนโลหะคือการวิเคราะห์การสึกหรอเพียงอย่างเดียว ซึ่งเน้นด้านการจัดการวัสดุของเครื่องมือ, รูปทรง และพารามิเตอร์การใช้งาน เพื่อปรับปรุงการผลิตชิ้นส่วน และอายุการใช้งานเครื่องมือ ในการดำเนินการเฉพาะ อย่างไรก็ตาม การเพิ่มประสิทธิภาพสูงสุดให้กระบวนการผลิตของทั้งโรงงานนั้นเป็นเรื่องการพิจารณาปัจจัยต่างๆ ในวงกว้างนอกเหนือจากการสึกหรอของเครื่องมือ การสำรวจการสึกหรอของเครื่องมือตัดเป็นสิ่งสำคัญ หรือโดยรวมแล้วก็คือ การเสื่อมสภาพของเครื่องมือ ให้เป็นไปตามกระบวนการผลิต “โดยรวม” นั่นเอง
การวิเคราะห์การเสื่อมสภาพของเครื่องมือโดยรวม (Global Tool Deterioration Analysis - GTDA) นั้นเป็นมากกว่าเพียงการวัดความสึกหรอของเครื่องมือขั้นพื้นฐาน โดยประกอบด้วยข้อพิจารณาเกี่ยวกับเครื่องมือ เช่น เวลาที่ใช้ในการจัดการ, ปัญหาอื่นๆ นอกจากการสึกหรอ, เศรษฐศาสตร์การผลิต, การจัดระเบียบโรงงาน, ทัศนคติส่วนตัว และสมมติฐาน, การจัดการสายธารคุณค่า และต้นทุนการผลิตทั้งหมด GTDA นั้นอิงกับการประเมินอย่างสม่ำเสมอของเครื่องมือตัดที่โรงงานผลิตจำนวนมากใช้ โดยทำการเลือกแบบสุ่มเพื่อสร้างภาพรวมของบทบาทโดยรวม ที่มีภายในโรงงานผลิต
กระบวนการผลิตโดยรวม
การศึกษาด้านการสึกหรอของเครื่องมือมักจำกัดอยู่เฉพาะเครื่องมือเพียงชิ้นเดียวที่ใช้ในการตัดเฉือนเฉพาะ อย่างไรก็ตามเพื่อให้ได้ประโยชน์สูงสุด เป็นสิ่งสำคัญที่จะสำรวจการสึกหรอของเครื่องมือ หรือการเสื่อมสภาพที่เกี่ยวกับการตัดเฉือนทั้งหมดในกระบวนการผลิตของโรงงาน กระบวนการผลิต (รูปที่ 2) เริ่มต้นด้วยการแสวงหาวัตถุดิบ และการวางแผนเกี่ยวกับการใช้สติปัญญาของมนุษย์ ทรัพยากรทางเทคโนโลยี และการลงทุนด้วยเงิน กระบวนการประกอบด้วยการเพิ่มมูลค่า และกิจกรรมที่สามารถเพิ่มมูลค่า แต่อาจพบอุปสรรค์จากการผลิตของเสียที่ทำให้เกิดความเสียหายทางการเงิน เวลาและทรัพยากรทรงภูมิปัญญา ส่งผลให้คุณภาพของชิ้นส่วน และผลผลิตลดลง ผลผลิตจะถูกวัดในแง่คุณภาพชิ้นส่วน ปริมาณที่ต้องการ และเวลาและต้นทุนในการผลิตที่ต้องการ
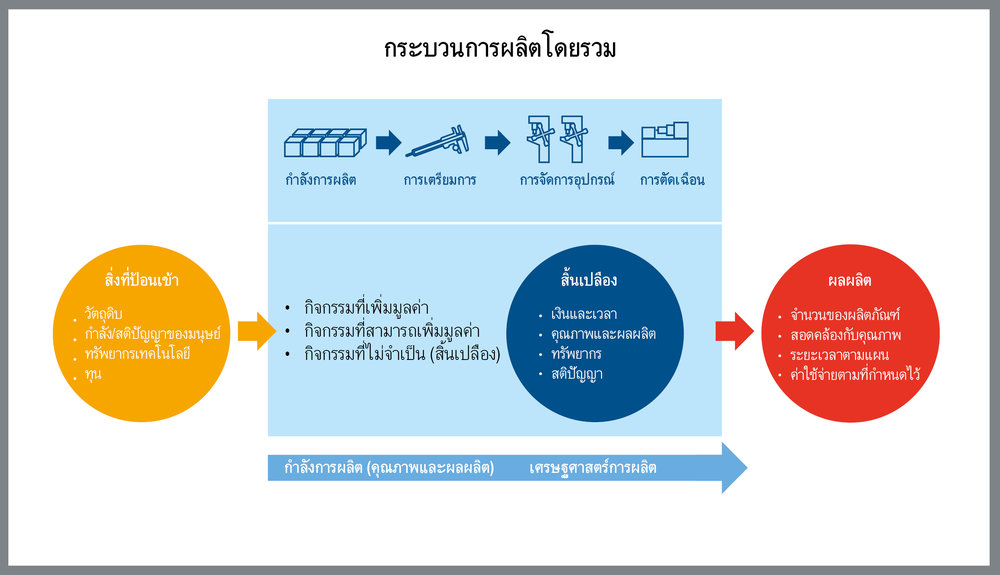
HQ_ILL_Global_Manufacturing_Process.jpg
รูปที่ 2
วิวัฒนาการของกระบวนการผลิต
วิธีที่ใช้วิเคราะห์และคาดการณ์อายุการใช้งานเครื่องมือนั้นขึ้นอยู่กับวิธีการนำเครื่องมือดังกล่าวมาใช้ เป็นเวลาหลายศตวรรษที่การผลิตได้พัฒนาจากการผลิตชิ้นงานด้วยมือ ไปเป็นการผลิตเป็นจำนวนมากของชิ้นส่วนที่มีมาตรฐานเดียวกัน การปรับปรุงวิธีการผลิตนำมาซึ่งยุคที่ 2 ของการผลิตเป็นจำนวนมากที่สามารถผลิตชิ้นส่วนที่คล้ายกันในปริมาณที่มากขึ้น ซึ่งเป็นสถานการณ์แบบ High Volume, Low Product Mix (HVLM) และล่าสุด การนำเทคโนโลยีดิจิตอลมาใช้ในการเขียนโปรแกรม ควบคุมเครื่องมือตัดเฉือน และระบบการจัดการชิ้นงานกำลังนำไปสู่ยุคที่ 3 ของการผลิตเป็นจำนวนมากที่ทำให้สามารถผลิตแบบ High-Mix Low-Volume (HMLV) ได้
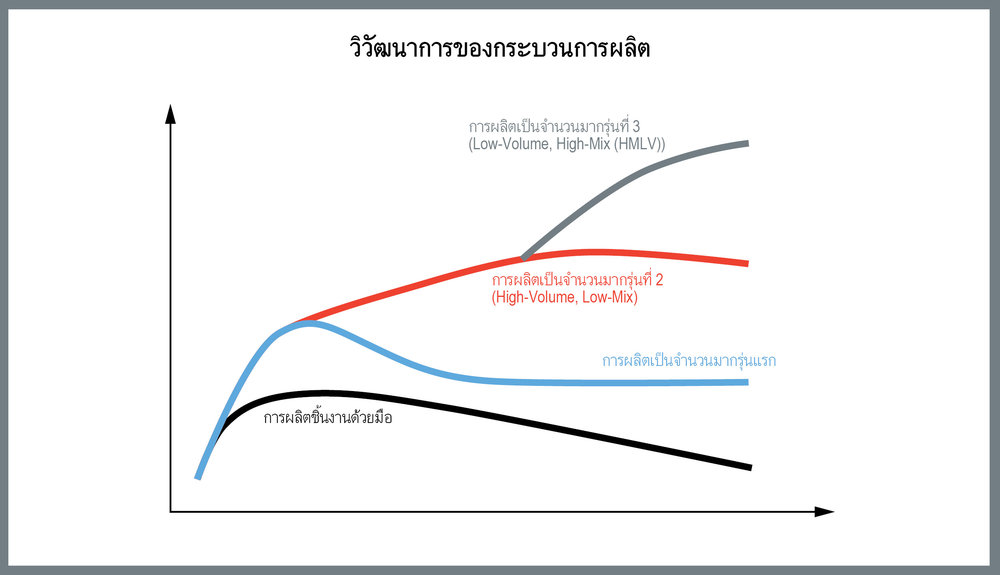
HQ_ILL_Manufacturing_Process_Evolution.jpg
รูปที่ 3
แม้ว่าจะยังคงมีปัญหาด้านประสิทธิภาพ กล่าวคือการประหยัดและความรวดเร็ว คุณภาพและผลผลิตขั้นต่ำ เทคนิคการผลิตเป็นจำนวนมากยุคที่ 2 และ 3 ต้องใช้วิธีการวิเคราะห์อายุการใช้งานเครื่องมือที่แตกต่างกัน ในสถานการณ์ HVLM ยุคที่ 2 ชิ้นส่วนที่เหมือนกันถูกตัดเฉือนจากวัสดุชิ้นงานเดียวกันในการผลิตซึ่งอาจใช้เวลาหลายวัน หลายเดือน หรือหลายปี โดยใช้อุปกรณ์ตัดประเภทเดียวกัน ซึ่งในสถานการณ์ดังกล่าว การจัดการอายุการใช้งานเครื่องมือนั้นเป็นสิ่งที่ง่าย พนักงานของโรงงานผลิตจะใช้การสร้างต้นแบบ และการทดสอบเพื่อหาอายุการใช้งานเครื่องมือเฉลี่ยที่ดีที่สุด แล้วหารอายุการใช้งานเครื่องมือที่คาดหวังด้วยจำนวนชิ้นส่วนที่ต้องการผลิต
ข้อมูลอายุคาดหวังของเครื่องมือที่สม่ำเสมอจะช่วยโรงงานในการวางแผนการเปลี่ยนเครื่องมืออย่างมีประสิทธิภาพสูงสุด และช่วยสนับสนุนการผลิตอย่างต่อเนื่อง อย่างไรก็ตาม วิธีการผลิตแบบ HVLM กลับมีบทบาทน้อยลง เพื่อสร้างสมดุลให้กับคลังชิ้นส่วนกับความต้องการและสนับสนุนการเปลี่ยนแปลงทางวิศวกรรมอย่างต่อเนื่อง ผู้ผลิตได้เปลี่ยนมาสู่การผลิตชิ้นส่วนที่น้อยลงในกระบวนการผลิตที่ยาวนานและคงที่
ในขณะเดียวกัน กลยุทธ์การผลิตเป็นจำนวนมากแบบ HMLV ยุคที่ 3 นั้นได้รับการยอมรับเพิ่มขึ้น กระบวนการ HMLV ที่ปรับได้อย่างรวดเร็วนั้นเข้ากันได้เป็นอย่างดีกับเป้าหมายด้านคลังชิ้นส่วนร่วมสมัยและด้านวิศวกรรม แต่มีกระบวนการวางแผนที่ซับซ้อนกว่ามาก การผลิตชิ้นส่วน 10 ชิ้นอาจตามมาด้วยการผลิตเป็นล็อต 3 หรือ 5 ชิ้น และแม้กระทั่งส่วนประกอบเพียงชิ้นเดียว โดยมีวัสดุชิ้นงานอันหลากหลาย ตั้งแต่เหล็กกล้า อะลูมิเนียม หรือไทเทเนียม และรูปทรงชิ้นส่วนตั้งแต่ง่ายไปจนถึงซับซ้อน เนื่องจากไม่มีเวลาในการหาอายุการใช้งานของเครื่องมือจากการทดลอง
ในกรณีดังกล่าวโรงงานมักคาดการณ์อายุการใช้งานของเครื่องมืออย่างระมัดระวัง และเพื่อความปลอดภัย มีการใช้เครื่องมือใหม่สำหรับการทำงานแต่ละครั้ง และทำการทิ้งก่อนที่เครื่องมือจะหมดอายุการใช้งานเป็นเวลานาน การวิเคราะห์และการคาดการณ์ความสึกหรอของเครื่องมือโดยรวมสามารถช่วยลดความสูญเสียด้านความสามารถของเครื่องมือตัดได้
ความเป็นไปได้ด้านผลผลิตที่ต้องเลือกอย่างใดอย่างหนึ่ง
การเปลี่ยนวิธีการผลิตแบบ HMLV อย่างรวดเร็วนั้นทำให้เป็นการยากยิ่งขึ้นที่จะบรรลุผลผลิตเป็นเปอร์เซ็นต์สูงในด้านการปฏิบัติการผลิต ในกรณีของการผลิต HVLM ที่ยาวนาน การทดลองและการปรับสามารถให้ผลผลิตเกือบ 100 เปอร์เซ็นต์ ในขณะเดียวกันผลผลิตในสถานการณ์ HMLV อาจเป็นแบบต้องเลือกอย่างใดอย่างหนึ่ง การผลิตชิ้นส่วนเพียงชิ้นเดียวที่ประสบความสำเร็จอาจถือได้ว่าบรรลุผลผลิต 100 เปอร์เซ็นต์ แต่เมื่อได้คุณภาพที่ไม่สามารถยอมรับได้ หรือชิ้นงานได้รับความเสียหาย นั่นคือผลผลิตเท่ากับศูนย์
ความต้องการด้านคุณภาพ ต้นทุน และความรวดเร็วนั้นยังคงเดิม แต่ผลผลิตครั้งแรกจะกลายเป็นความต้องการที่เหนือกว่าสิ่งใด ในกรณีดังกล่าว การหลีกเลี่ยงการชำรุดของเครื่องมืออาจเป็นข้อพิจารณาที่มีความสำคัญสูงสุด ข้อได้เปรียบประการหนึ่งคือไม่ต้องกังวลมากนักเรื่องการสึกหรอของเครื่องในการทำงานระยะสั้น และหากมีเหตุผลที่ดี โรงงานสามารถนำพารามิเตอร์การตัดที่รุนแรงและมีประสิทธิภาพยิ่งขึ้นมาใช้ได้
คุณภาพของงานและบทบาทของคน
การผลิตแบบ HVLM ที่ยาวนานและคงที่นั้นมีแนวโน้มที่จะลดความสำคัญของบทบาทของคนต่อกระบวนการผลิต เมื่อกระบวนการผลิตที่ยาวนานเริ่มขึ้น การดำเนินงานสามารถเป็นไปโดยอัตโนมัติ แม้ในกรณีที่ผู้ควบคุมมีส่วนร่วมในทุกการเปลี่ยนแปลงระหว่างชิ้นส่วน ความซ้ำซ้อนของสถานการณ์เหล่านี้ลดความสำคัญของอิทธิพลของผู้ควบคุมและผู้โปรแกรม ทั้งนี้ไม่ต้องการความยืดหยุ่น และบางทีไม่ควรมีด้วยซ้ำ
ในทางกลับกันสถานการณ์ HMLV ที่เปลี่ยนแปลงอย่างรวดเร็วตอกย้ำให้เห็นความสำคัญของคนในกระบวนการผลิต ถึงระดับที่ผู้ควบคุมต้องการรูปแบบฝีมือแบบดั้งเดิมในด้านความคิดสร้างสรรค์และความยืดหยุ่นเพื่อการปรับตัวอย่างมีประสิทธิภาพให้เหมาะสมกับชิ้นส่วน และคุณลักษณะเงื่อนไขการตัดแบบ HMLV ที่มีการเปลี่ยนแปลงอย่างต่อเนื่อง
ให้ความสำคัญกับกระบวนการก่อนผลลัพธ์
ความพยายามในการวิเคราะห์กระบวนการผลิตจำนวนมากนั้นมุ่งเน้นไปที่การตรวจสอบผลลัพธ์สุดท้าย ที่เกี่ยวกับอายุการใช้งานของเครื่องและผลผลิตชิ้นส่วน โดยไม่ได้สำรวจกระบวนการอย่างละเอียด ทั้งนี้ อาจพลาดพลั้งในเรื่องเครื่องมือตัด แต่ไม่เกี่ยวข้องโดยตรงกับอายุการใช้งานเครื่อง ทำให้เกิดปัญหาคอขวดในการผลิต ตัวอย่าง เช่น การเกิดเสี้ยน ซึ่งมักไม่เกี่ยวกับอายุการใช้งานเครื่องมือ แต่เป็นสิ่งรบกวนกระบวนการผลิต เพราะต้องพัฒนาและนำกระบวนการอย่างอื่นมาใช้ในการขจัดเสี้ยน
อย่างไรก็ตาม การเกิดเสี้ยนเป็นเรื่องเกี่ยวกับรูปทรงของเครื่องมือและพารามิเตอร์การใช้งาน ซึ่งต้องพิจารณาเป็นปัจจัยหนึ่งในการวิเคราะห์การเสื่อมสภาพของเครื่องมือ การชำรุดของเครื่องมือ เป็นอีกปัญหาหนึ่งที่มักไม่เกี่ยวกับการสึกหรอของเครื่องมือ แต่เกี่ยวกับวัสดุ รูปทรง พารามิเตอร์การใช้ รวมไปถึงปัจจัยของเครื่องตัดเฉือน
องค์ประกอบของความเป็นเลิศในการปฏิบัติงาน
องค์ประกอบพื้นฐานของประสิทธิภาพการผลิต คือการขจัดความสิ้นเปลือง, ความไม่ยืดหยุ่น และความผันแปร การวิเคราะห์การเสื่อมสภาพของเครื่องมืออย่างครอบคลุมจะพิจารณา 5 องค์ประกอบของความเป็นเลิศในการปฏิบัติงาน
อันดับแรก เป็นสิ่งสำคัญที่ต้องทำความเข้าใจอย่างละเอียดเรื่องกระบวนการตัดเฉือนโดยรวม และความสัมพันธ์ของการดำเนินการตัดเฉือนกับวัสดุชิ้นงาน อันดับที่ 2 ต้องให้ความใส่ใจในการลดของเสีย ด้วยการใช้กลยุทธ์การผลิตอย่างมีประสิทธิภาพและการริเริ่มอื่นๆ อันดับที่ 3 ต้องนำแนวคิดเศรษฐศาสตร์การผลิตมาใช้ เพื่อให้เกิดผลกำไร อันดับที่ 4 ควรพิจารณาเป้าหมายเปอร์เซ็นต์ผลผลิตโดยใช้ปริมาณการผลิตและความหลากหลายของชิ้นส่วน ต้องพิจารณาความยืดหยุ่นสูงสุดเป็นวิธีในการลดปัญหาคอขวด แต่ต้องควบคุมความผันแปรเพื่อให้ได้ชิ้นส่วนที่มีคุณภาพเสมอต้นเสมอปลาย อันดับสุดท้าย จำเป็นต้องให้ความสำคัญกับบุคคลากรการผลิตเพื่อให้ได้ประโยชน์สูงสุดจากทรัพยากรที่โดดเด่นและไม่สามารถทดแทนได้
ข้อควรพิจารณานอกเหนือจากการสึกหรอของเครื่องมือ
การวิเคราะห์เครื่องมือโดยรวมช่วยส่งเสริมการวัดการสึกหรอของคมตัดเม็ดมีดเบื้องต้นด้วยการวิเคราะห์บทบาทของเครื่องมือในผลรวมต้นทุนของสินค้าที่จำหน่าย (Cost of Goods Sold - COGS) , การวิเคราะห์การปรับเปลี่ยนเครื่องจักรอย่างรวดเร็ว (Single-Minute Exchange of Die - SMED), ผลลัพธ์ของสายธารคุณค่า (Value Stream Management - VSM) และเปอร์เซ็นต์ของประสิทธิภาพอุปกรณ์โดยรวม (Overall Equipment Effectiveness - OEE)
ข้อพิจารณาด้านเศรษฐศาสตร์เกี่ยวกับการตัดเฉือนขั้นพื้นฐานที่สุดนั้นมีความชัดเจน นั่นคือ ต้นทุนด้านเครื่องมือ รูปที่ 4 แสดงให้เห็นต้นทุนของส่วนประกอบต่างๆ ของกระบวนการตัดเฉือน และนำมารวมกันเป็น COGS ข้อมูลเหล่านี้ช่วยโรงงานในการเปรียบเทียบองค์ประกอบต่างๆ ของต้นทุนการผลิต พร้อมกับแสวงหาปัจจัยในการลดต้นทุนที่จะช่วยเพิ่มผลกำไรในการดำเนินการ
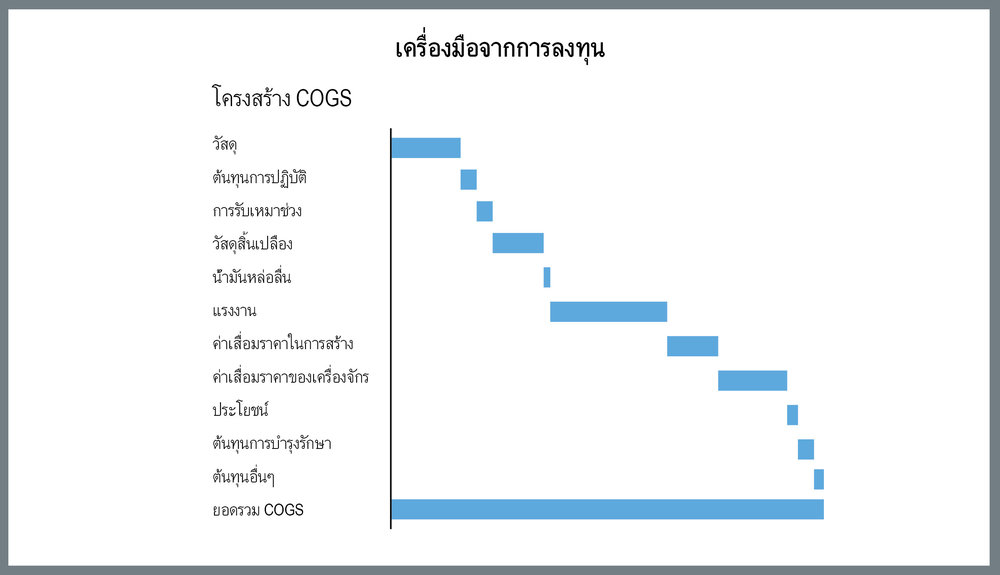
HQ_ILL_Tools_Cost_Money.jpg
รูปที่ 4
อีกปัจจัยด้านเศรษฐศาสตร์เกี่ยวกับเครื่องมือก็คือ เครื่องมือเป็นสิ่งต้องใช้เวลา เวลาในการจัดการการตัดเฉือนนอกเหนือจากการดำเนินการตัดเฉือนที่แท้จริง เวลาที่ใช้ในการเปลี่ยนเครื่องมือ และการตั้งค่าจะถูกวิเคราะห์ด้วยเทคนิคการวิเคราะห์แบบ SMED ที่ให้มุมมองต้นทุนนอกเหนือไปจากที่เกิดจากการสึกหรอและการเปลี่ยนเครื่องมือ ส่วนหนึ่งของค่าใช้จ่ายดังกล่าวเกิดจากการแสวงหา, การจัดระเบียบ, การติดตั้งเครื่องมือ และการโหลดโปรแกรมลงในเครื่องจักร
OEE จะระบุว่าเวลาในการผลิตเท่าใดที่ถูกใช้อย่างมีประสิทธิภาพ การวิเคราะห์ OEE จะชี้ให้เห็นความสูญเสีย, วัดความคืบหน้า และปรับปรุงประสิทธิภาพด้วยการขจัดความสิ้นเปลือง จะทำการระบุเวลาทั้งหมดที่ใช้ในการผลิต แล้วการวิเคราะห์จะทำการหักเวลาที่หยุดทำงาน, การชำรุดที่คาดไม่ถึง, การเปลี่ยนแปลง, การหยุดขนาดเล็ก และการสูญเสียความเร็ว และการแก้ไขชิ้นงานเพื่อให้ได้เวลาการตัดเฉือนที่มีประสิทธิภาพที่แสดงในรูปของเปอร์เซ็นต์ของเวลาทั้งหมดที่มี OEE 100 เปอร์เซ็นต์ คือเป้าหมายระดับสูง แต่ไม่สามารถบรรลุได้ในการปฏิบัติ หมายถึงชิ้นส่วนที่ผลิตตามคุณภาพที่ระบุ อย่างเร็วที่สุดเท่าที่ทำได้ โดยไม่เสียเวลาเลย
การวิเคราะห์ VSM จะแสดงให้เห็นความจำเป็นในการสร้างความสมดุลให้กับการปรับปรุงประสิทธิภาพของทุกองค์ประกอบของกระบวนการผลิต รูปที่ 5 คือภาพแสดงผลกระทบของการปรับปรุงประสิทธิภาพขององค์ประกอบเดียวของระบบ โดยไม่ปรับปรุงส่วนอื่นๆ คิดถึงภาพคนหลายคนที่พายเรือ หากฝีพายคนหนึ่งมีประสิทธิภาพการพายสูงกว่าคนอื่นย่อมส่งผลเสียต่อประสิทธิภาพโดยรวมของเรือ
ต้องทำการปรับปรุงส่วนต่างๆ ของกระบวนการอย่างสัมพันธ์กับปริมาณและความหลากหลายในการผลิต, คุณลักษณะของวัสดุชิ้นงาน, รูปทรงของชิ้นส่วน, เครื่องมือตัดเฉือน และความต้องการด้านการจับยึด และข้อควรพิจารณาอื่นๆ เพื่อบรรลุและคงไว้ซึ่งการดำเนินการผลิตโดยรวมที่สมดุล
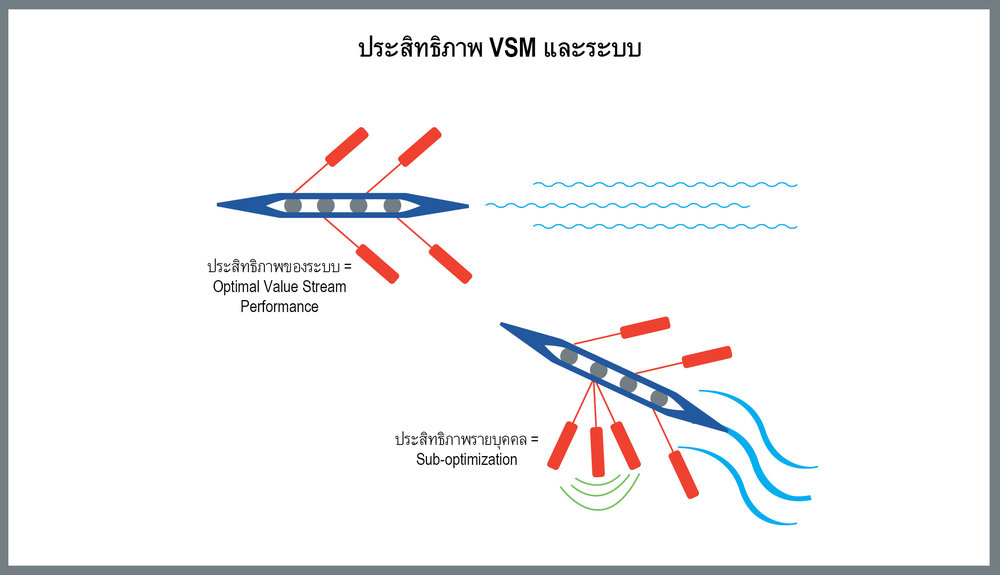
HQ_ILL_VSM_And_System_Efficiency.jpg
รูปที่ 5
การวิเคราะห์การเสื่อมสภาพของเครื่องมือโดยรวม
GTDA เป็นกระบวนการที่ง่าย คมตัดของเครื่องมือจำนวนมากที่ถูกเลือกแบบสุ่มจากทั่วทั้งโรงงานจะถูกนำมาตรวจสอบทีละ 1 คมตัดเพื่อหาว่าคมตัดใดที่สึกหรอ การสึกหรอจะถูกจัดประเภทตามชนิดและระดับการสึกหรอ การวิเคราะห์การสึกหรอของเครื่องมือแบบดั้งเดิมนั้นให้ความสำคัญกับเครื่องมือเพียง 1 ชิ้นใน 1 การดำเนินการ GTDA จะรวบรวมข้อมูลเกี่ยวกับการสึกหรอของเครื่องมือและปัญหาอื่นๆ เกี่ยวกับเครื่องมือจากทั้งโรงงาน แล้วนำเครื่องมือการวิเคราะห์ COGS, SMED, VSM, OEE และอื่นๆ มาใช้ เพื่อประกอบเป็นข้อมูลเพิ่มเติมที่ใช้เป็นแนวทางการวางแผนและการนำโปรแกรมการปรับปรุงมาใช้
เพื่อที่จะประสบความสำเร็จ โรงงานต้องมีวินัยในการเริ่มโปรแกรม GTDA และที่สำคัญไม่ยิ่งหย่อนไปกว่ากัน คือ ทำการสำรวจเครื่องมือ และวิเคราะห์ข้อมูลเป็นประจำ อีกรูปแบบหนึ่งของวินัย คือความจริงใจ ซึ่งเป็นที่ต้องการเช่นกัน โรงงานต้องยอมรับผลการวิเคราะห์อย่างจริงใจและไม่ลำเอียง และเต็มใจที่จะดำเนินการตามผลการวิเคราะห์โดยไม่คำนึงถึงแนวทางปฏิบัติและการเมือง หรือความคิดเห็นที่ไม่ได้รับการสนับสนุนเกี่ยวกับพารามิเตอร์การใช้งานเครื่องมือ
บทสรุป
การสึกหรอของเครื่องมือเป็นสิ่งที่หลีกเลี่ยงไม่ได้ และการจัดการเป็นสิ่งจำเป็นต่อการประสบความสำเร็จในการตัด
เฉือน อย่างไรก็ตามการสึกหรอของเครื่องมือเป็นเพียงตัวอย่างหนึ่งของอิทธิพลจำนวนมากของเครื่องมือตัดต่อประสิทธิภาพของกระบวนการผลิตโดยรวมของโรงงาน GTDA ก้าวล้ำไปมากกว่าการวิเคราะห์การสึกหรอของเครื่องมือเพียงชิ้นเดียว และทำการรวมเครื่องมือทั้งหมดในโรงงาน รวมไปถึงอิทธิพลอันหลากหลายที่สำคัญที่เกี่ยวกับเครื่องมือนอกเหนือจากกระบวนการตัด
แถบด้านข้าง:
GTDA: เหตุผลและวิธี
ที่จุดสูงสุดของยุคการผลิตชิ้นส่วนทีละชิ้นเป็นจำนวนมาก การสึกหรอของเครื่องมือจะถูกวัด จัดการ และสร้างความสมดุลเพื่อยืดอายุการใช้งานเครื่องมือให้ยาวนานที่สุดและเพิ่มการผลิตชิ้นส่วนให้ได้สูงสุด ขณะที่กลยุทธ์การผลิตก้าวหน้าไปสู่การผลิตแบบทันเวลาพอดีของชิ้นส่วนที่เกือบจะเป็นแบบกำหนดเอง การสึกหรอของเครื่องมือโดยตัวมันเองนั้นจะไม่ใช่องค์ประกอบที่สำคัญที่สุดโดยรวม
บริการให้คำปรึกษาของ Seco ทำการวิเคราะห์วิวัฒนาการการผลิตที่กำลังดำเนินอยู่อย่างต่อเนื่อง และได้พัฒนาแบบจำลองการผลิตแบบ
“NEXT STEP” เพื่อรับมือกับการเปลี่ยนแปลงที่เกิดขึ้นอย่างต่อเนื่องในอุตสาหกรรมการผลิต (รูปที่ 6) แบบจำลอง NEXT STEP นั้นอิงกับมาตรฐานการตัดเฉือนหลัก 4 ประการ ได้แก่ ประสิทธิภาพการใช้ต้นทุน, ประสิทธิภาพการใช้เวลา, คุณภาพ และผลผลิต Next Step ช่วยผู้ผลิตในการตั้งค่า และบรรลุมาตรฐานการตัดเฉือนของตนเองผ่านการวิเคราะห์การสร้างของเสีย, เทคโนโลยีการดำเนินการตัดเฉือน, วิทยาศาสตร์วัสดุชิ้นงานและเครื่องมือ, เศรษฐกิจการผลิตและผลผลิต และบทบาทที่สำคัญของผู้คนและความเป็นผู้นำในการดำเนินการ
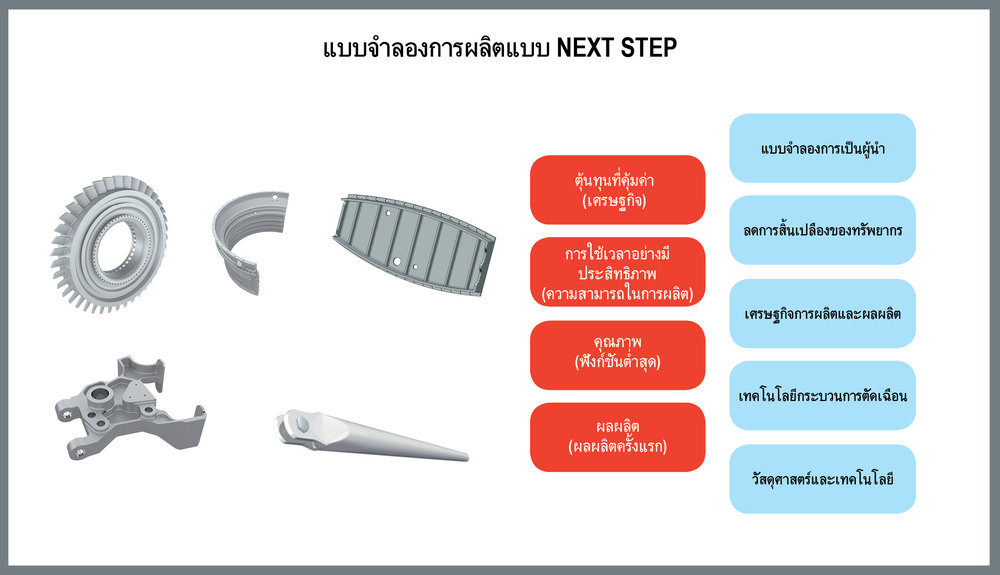
HQ_ILL_Next_Step_Production_Model.jpg
รูปที่ 6
Global Tool Deterioration Analysis (รูปที่ 7) คือองค์ประกอบสำคัญของการประเมินและการปรับปรุงกระบวนการผลิตโดยรวม โดยสำรวจเครื่องมือที่ถูกสุ่มเลือกมาโดยครอบคลุมการตัดเฉือนทุกรูปแบบภายในโรงงาน แล้วนำการวัดผลการผลิตต่างๆ มาใช้ ผู้ผลิตจะเกิดความเข้าใจเชิงกว้างของบทบาทเครื่องมือในกระบวนการตัดเฉือนทั้งหมด GTDA ช่วยให้โรงงานค้นพบจุดที่สามารถปรับปรุงประสิทธิภาพของเครื่องมือเพื่อเพิ่มผลผลิตได้ และทราบถึงปัญหาคอขวดในการผลิตที่ทำให้สิ้นเปลืองเวลาและเงินอันเนื่องมาจากเครื่องมือ
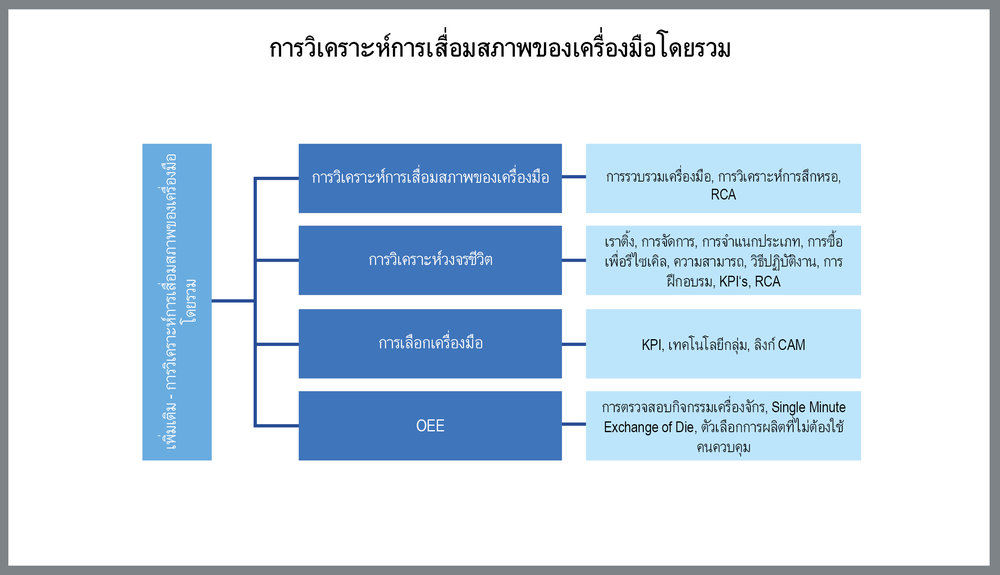
HQ_ILL_Global_Tool_Deterioration_Analysis.jpg
รูปที่ 7
ในเรื่องเฉพาะของ GTDA, Seco Consulting Services ได้เขียนตำราชื่อ “Tool Deterioration: Best Practices” (รูปที่ 8) ซึ่งนำเสนอการเสื่อมสภาพของเครื่องมือเป็นจุดดุลยภาพสำหรับแบบจำลองความสามารถในการตัดเฉือน โดยยอมรับว่าปัญหาส่วนใหญ่ในกระบวนการตัดเฉือนสามารถจัดประเภทได้เป็นเหตุการณ์ที่เกี่ยวกับการเสื่อมสภาพของเครื่องมือ แนวทางนี้กล่าวถึงการใช้งานต่างๆ ในการตัดเฉือนโลหะ และเพื่อให้ข้อมูลเชิงลึกเกี่ยวกับปรากฏการณ์ที่ทำให้เครื่องมือเสื่อมสภาพ ในขณะที่ยังนำเสนอภาพรวมของ “แนวทางปฏิบัติที่ดีที่สุด” ในการระบุ จัดการ และควบคุมกระบวนการเสื่อมสภาพของเครื่องมือ
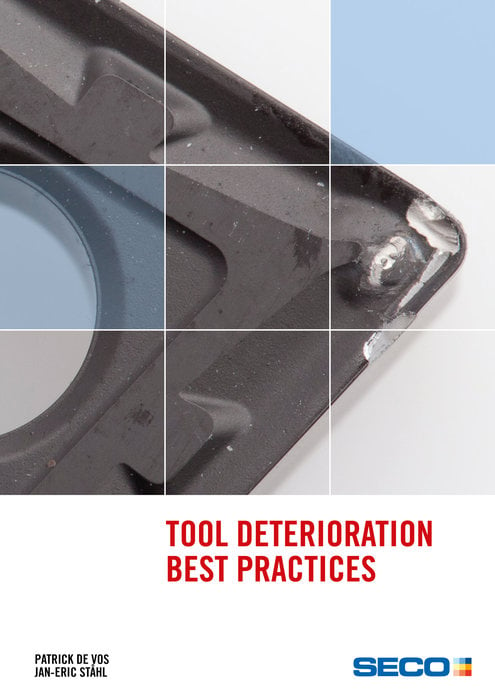
HQ_IMG_Tool_Deterioration_Best_Practices_2014.jpg
รูปที่ 8
จัดทำโดย:
Patrick de Vos ผู้จัดการฝ่ายการศึกษาทางเทคนิคของบริษัท Seco Tools